Die Casting Machine Factories: The Backbone of Precision Manufacturing
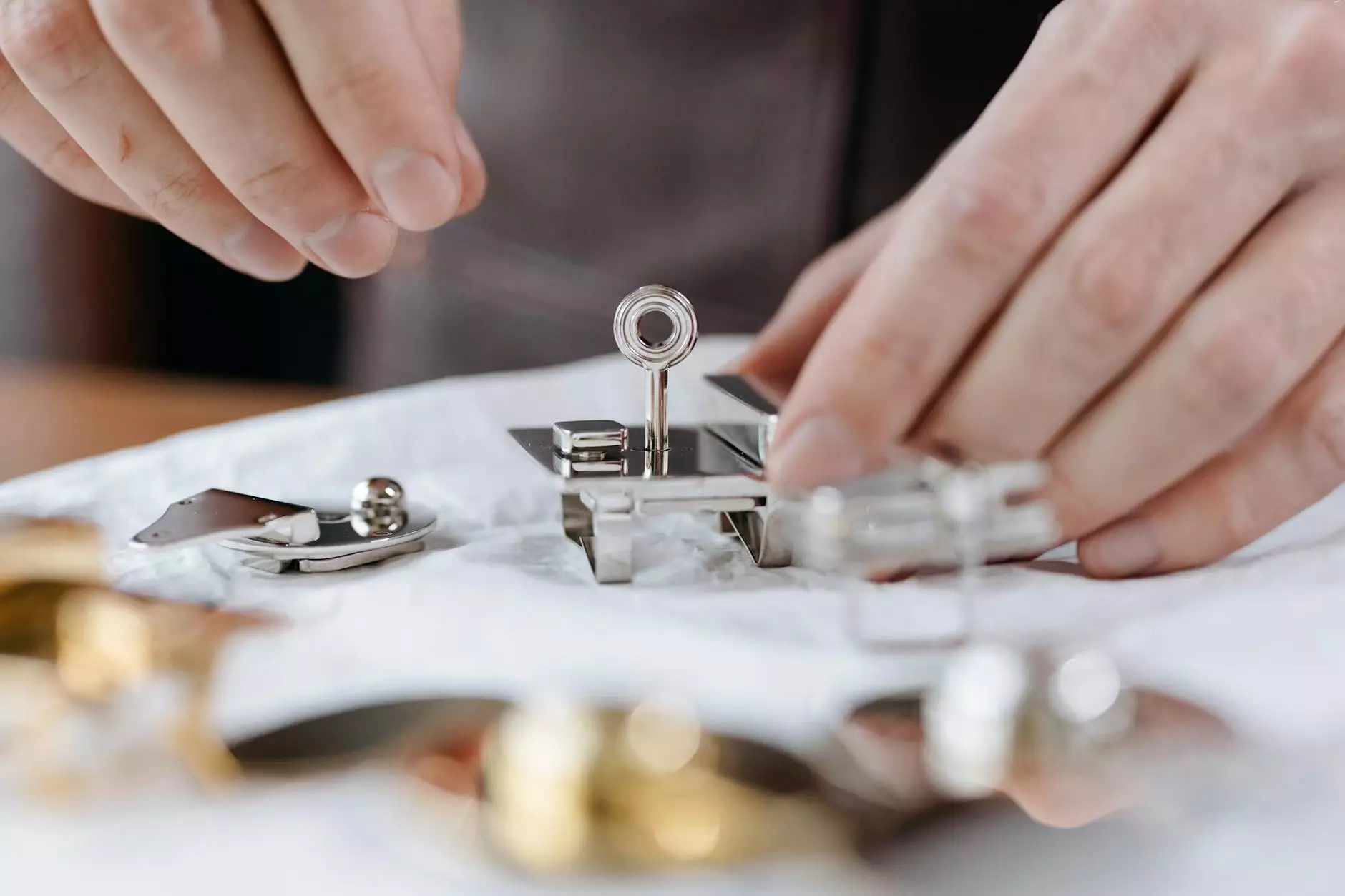
In today's industrial landscape, die casting machine factories play a crucial role in the production of high-quality metal components. These factories are equipped with advanced technology that allows for the mass production of intricate parts, meeting the demands of various industries such as automotive, electronics, and aerospace. In this comprehensive article, we will delve deep into the significance of die casting machine factories, their processes, advantages, and future prospects.
Understanding Die Casting
Die casting is a metal casting process characterized by forcing molten metal under high pressure into a mold cavity. The molds, referred to as die, are made from steel and designed to produce complex shapes with tight tolerances. This process is used for various materials like zinc, aluminum, magnesium, and copper.
The Die Casting Process
The die casting process typically involves several key steps:
- Preparation: The die is prepared with a release agent to facilitate the removal of the finished part.
- Melting: The metal alloy is heated to its molten state.
- Injection: Molten metal is injected into the die at high pressure, filling the mold cavity.
- Cooling: The molten metal cools rapidly, solidifying into the desired shape.
- Ejection: The die is opened, and the finished part is ejected from the mold.
- Finishing: Additional finishing processes may be applied, like trimming, machining, or polishing.
The Advantages of Die Casting
Die casting offers numerous advantages that make it a preferred manufacturing method for many industries:
- High Precision: Achieves tight tolerances and complex geometries, ensuring high-quality parts.
- Mass Production: Ideal for large production runs, reducing the cost per unit significantly.
- Excellent Surface Finish: Produces smooth surfaces, often requiring minimal post-processing.
- Material Efficiency: Minimizes waste, as the process is designed to maximize the use of every drop of molten metal.
- Rapid Production Speed: Quick cycle times enhance production rates without compromising quality.
Industry Applications of Die Casting
Die casting is widely used in various industries. Here are some of the major applications:
Automotive Industry
In the automotive sector, die casting is essential for producing components such as:
- Engine blocks
- Transmission housings
- Suspension components
- Intake manifolds
The strength and lightweight nature of die cast parts contribute to the overall efficiency and performance of vehicles.
Electronics Industry
Die casting also plays a significant role in manufacturing metal parts for electronic devices, including:
- Heatsinks
- Housing for electrical components
- Connectors and terminals
The ability to produce intricate designs leads to better thermal management and enhanced performance in electronics.
Aerospace Industry
In aerospace, where safety and reliability are paramount, die casting is utilized for:
- Engine components
- Structural parts
- Fasteners and fittings
The lightweight yet robust nature of die cast components helps to meet strict regulatory standards while improving fuel efficiency.
Die Casting Machine Factories: Key Players in the Industry
Die casting machine factories are specialized facilities where the die casting process takes place. They play a vital role in ensuring the quality and efficiency of production. Here’s what sets exemplary die casting machine factories apart:
Advanced Machinery
Top-tier die casting machine factories are equipped with the latest technologies, including:
- High-pressure die casting machines
- Robotic automation for precision handling
- Advanced temperature control and monitoring systems
These innovations lead to improved accuracy, reduced cycle times, and lower production costs.
Expert Engineering Teams
The success of a die casting factory hinges on its skilled workforce. Engineers and operators must understand:
- The metallurgy of different alloys
- Precision machining techniques
- Quality control measures
An expert team ensures that the factory’s operations run smoothly and efficiently, from design to production.
Quality Control in Die Casting Machine Factories
Quality assurance is critical in die casting to ensure products meet specified standards. Here are some common quality control practices:
Inspection Techniques
Die casting machine factories typically employ various inspection techniques, including:
- Visual inspection for surface defects
- Dimensional measurement using coordinate measuring machines (CMM)
- Non-destructive testing methods to detect internal flaws
These practices help in maintaining high-quality standards and preventing defects from reaching the customer.
Traceability and Documentation
Establishing a robust traceability system is essential. This involves:
- Tracking raw materials through production
- Documenting processes and inspections
- Maintaining quality reports for compliance
Such measures ensure accountability and facilitate continuous improvement in manufacturing processes.
The Future of Die Casting Machine Factories
The landscape of die casting is evolving rapidly. Several trends are shaping the future of die casting machine factories:
Digital Transformation
As Industry 4.0 continues to influence manufacturing, die casting facilities are adopting digital technologies, including:
- Internet of Things (IoT) for real-time monitoring
- Big Data analytics for process optimization
- Artificial Intelligence (AI) for predictive maintenance
This shift leads to smarter factories, where machines communicate and optimize their performance, enhancing overall productivity.
Sustainability Initiatives
With environmental regulations becoming stringent, die casting machine factories are increasingly focusing on sustainability by:
- Implementing energy-efficient processes
- Recycling scrap metal and minimizing waste
- Using eco-friendly materials and coatings
These initiatives not only reduce environmental impact but also appeal to eco-conscious consumers and businesses.
Conclusion
In conclusion, die casting machine factories are integral to modern manufacturing, providing unmatched precision and efficiency in producing metal components. With their advanced technologies, skilled workforce, and commitment to quality, these factories will continue to drive innovation across various industries. As they embrace digital transformations and sustainability, the future of die casting looks promising, ensuring that they remain at the forefront of manufacturing excellence.
For more insights and a deeper understanding of metal fabrication and die casting processes, visit us at Deep Mould.