The Essential Role of Pumps in Hydraulics
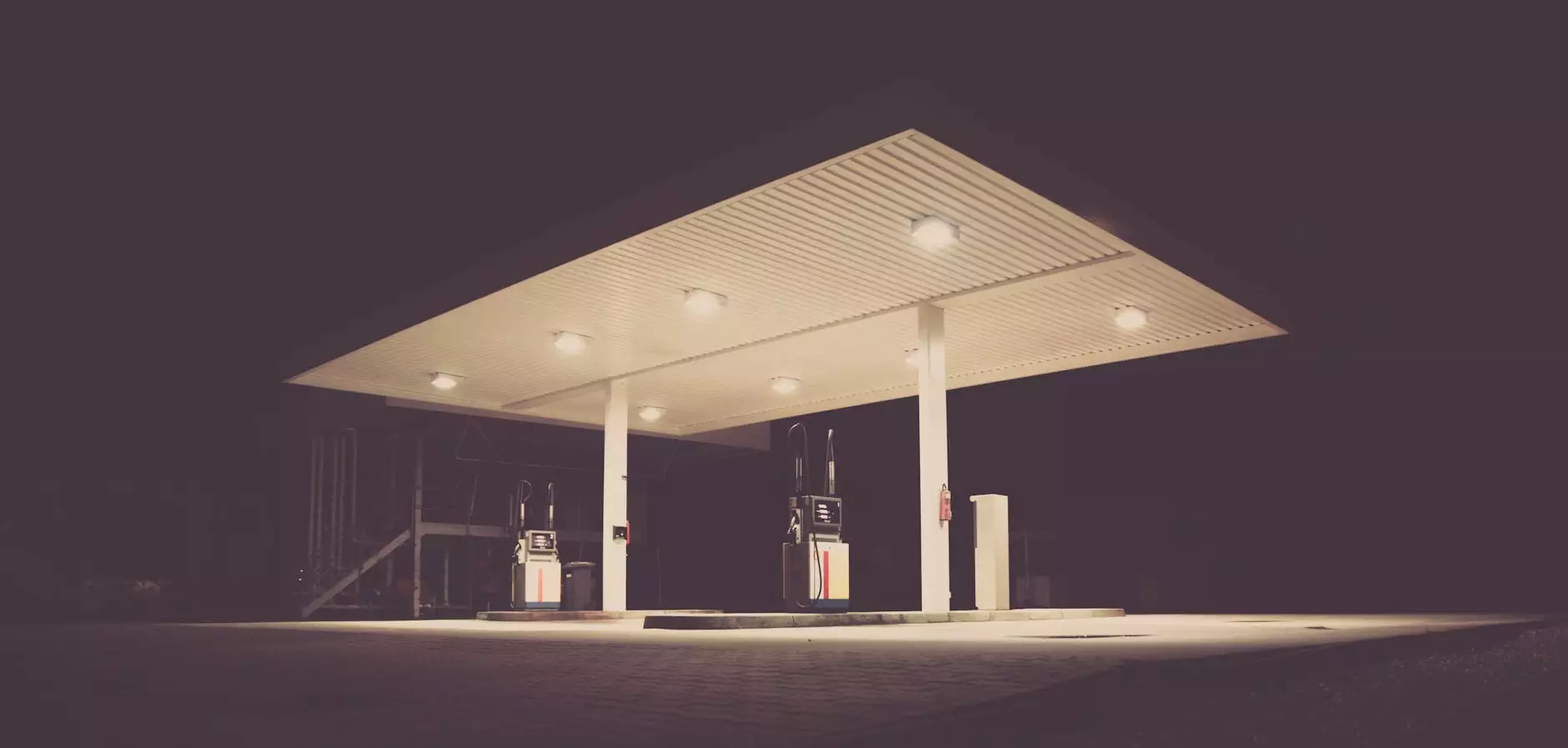
Understanding pumps in hydraulics is crucial for anyone involved in industries that rely on fluid power systems. These pumps are not only the lifeblood of hydraulic systems, but they also play a significant role in ensuring the efficiency and effectiveness of hydraulic machinery. In this extensive article, we will explore various aspects of hydraulic pumps, their types, functions, applications, and how they contribute to the world of auto and motorcycle parts and supplies.
What are Hydraulic Pumps?
Hydraulic pumps are mechanical devices that convert mechanical energy into hydraulic energy by creating flow within hydraulic fluid. They are essential components in hydraulic systems, providing the necessary pressure to move actuators, motors, and other hydraulic components.
Types of Hydraulic Pumps
There are several types of hydraulic pumps used in various applications. Understanding these varieties is key to selecting the right pump for specific needs. Below are the primary types of hydraulic pumps:
- Gear Pumps: These pumps use gears to pump fluid by displacement. They are simple, compact, and robust, making them suitable for various applications.
- Vane Pumps: Utilizing a series of vanes to generate flow, vane pumps are often used for moderate-pressure operations. They offer smooth operation and are typically quieter than gear pumps.
- Piston Pumps: Known for their efficiency and ability to handle high pressures, piston pumps can be axial or radial. They are often found in heavy-duty applications, including construction and manufacturing.
- Diaphragm Pumps: Ideal for transferring fluids that could harm the pump, diaphragm pumps use a flexible membrane to draw liquid in and push it out, making them suitable for various applications in different industries.
How Pumps in Hydraulics Work
The core function of pumps in hydraulics lies in their ability to generate flow. When a hydraulic pump operates, it creates a vacuum on the inlet side, allowing hydraulic fluid to flow into the pump. The mechanism inside the pump, depending on its type, then forces the fluid out into the hydraulic circuit, creating the pressure necessary to perform work.
The Hydraulic Cycle
The hydraulic cycle typically involves the following steps:
- The pump draws hydraulic fluid from the reservoir.
- The mechanism within the pump compresses and moves the fluid under pressure.
- The pressurized fluid is directed towards actuators or hydraulic motors.
- Finally, the fluid returns to the reservoir to repeat the cycle.
Applications of Hydraulic Pumps
Hydraulic pumps have a wide range of applications across various industries. Their versatility makes them indispensable in many areas. Here are some key applications:
- Construction: Hydraulic pumps are used in heavy machinery such as excavators, bulldozers, and cranes, where they provide the power to lift and move heavy loads.
- Automotive Industry: In automotive systems, hydraulic pumps are integral in brake systems, power steering, and suspension systems, ensuring smooth operation and safety.
- Aerospace: The aerospace sector relies on hydraulic pumps for aircraft systems, including landing gear and flight control surfaces, where precise pressure control is crucial.
- Manufacturing: Many manufacturing processes utilize hydraulic pumps for various tasks, including metal forming, injection molding, and material handling.
- Motorcycles: Hydraulic pumps play a vital role in motorcycle brake systems, enhancing control and safety on the road.
Benefits of Hydraulic Pumps
Using hydraulic pumps offers numerous benefits that make them a popular choice in various applications:
- High Efficiency: Hydraulic pumps can transmit significant power through small tubes, resulting in high efficiency and reduced energy loss.
- Precision Control: The ability to control hydraulic fluid flow and pressure allows for precise operation of machinery.
- Durability: Quality hydraulic pumps can withstand harsh conditions and provide reliable performance over time.
- Versatility: Hydraulic pumps can be used in numerous applications, making them suitable for a wide range of industries.
Choosing the Right Hydraulic Pump
Selecting the appropriate hydraulic pump is critical for the success of any fluid power system. Several factors must be considered during this process, including:
1. Application Requirements
Understand the specific needs of the application, including required flow rate, pressure, and the type of fluid to be used.
2. Efficiency
Choose pumps that offer high efficiency to minimize energy costs and optimize performance.
3. Compatibility
Ensure that the pump is compatible with other components within the hydraulic system.
4. Maintenance
Consider the maintenance requirements of the pump, including ease of access for repairs and the availability of replacement parts.
Maintenance Tips for Hydraulic Pumps
To ensure the longevity and performance of hydraulic pumps, proper maintenance is essential. Here are some tips for maintaining hydraulic pumps:
- Regular Inspection: Periodically inspect the pump for signs of wear, leaks, or damage.
- Fluid Quality: Ensure the hydraulic fluid is clean and free from contaminants to prevent pump failure.
- Check for Overheating: Monitor pump temperature and address any overheating issues promptly.
- Lubrication: Keep moving parts lubricated according to the manufacturer's guidelines.
Conclusion
In conclusion, pumps in hydraulics are vital components that power a wide range of machinery and applications across various industries. Understanding their operation, types, and benefits can lead to better decision-making when selecting and maintaining hydraulic systems. For those involved in the automotive and motorcycle parts industry, incorporating reliable hydraulic pumps can significantly enhance performance and safety. Investing in high-quality hydraulic components from reputable suppliers, such as Shop Hydraulic America, will ensure that you are well-equipped to harness the full potential of hydraulic technology in your operations.