Understanding Metal Die Casting: A Gateway to Precision Manufacturing
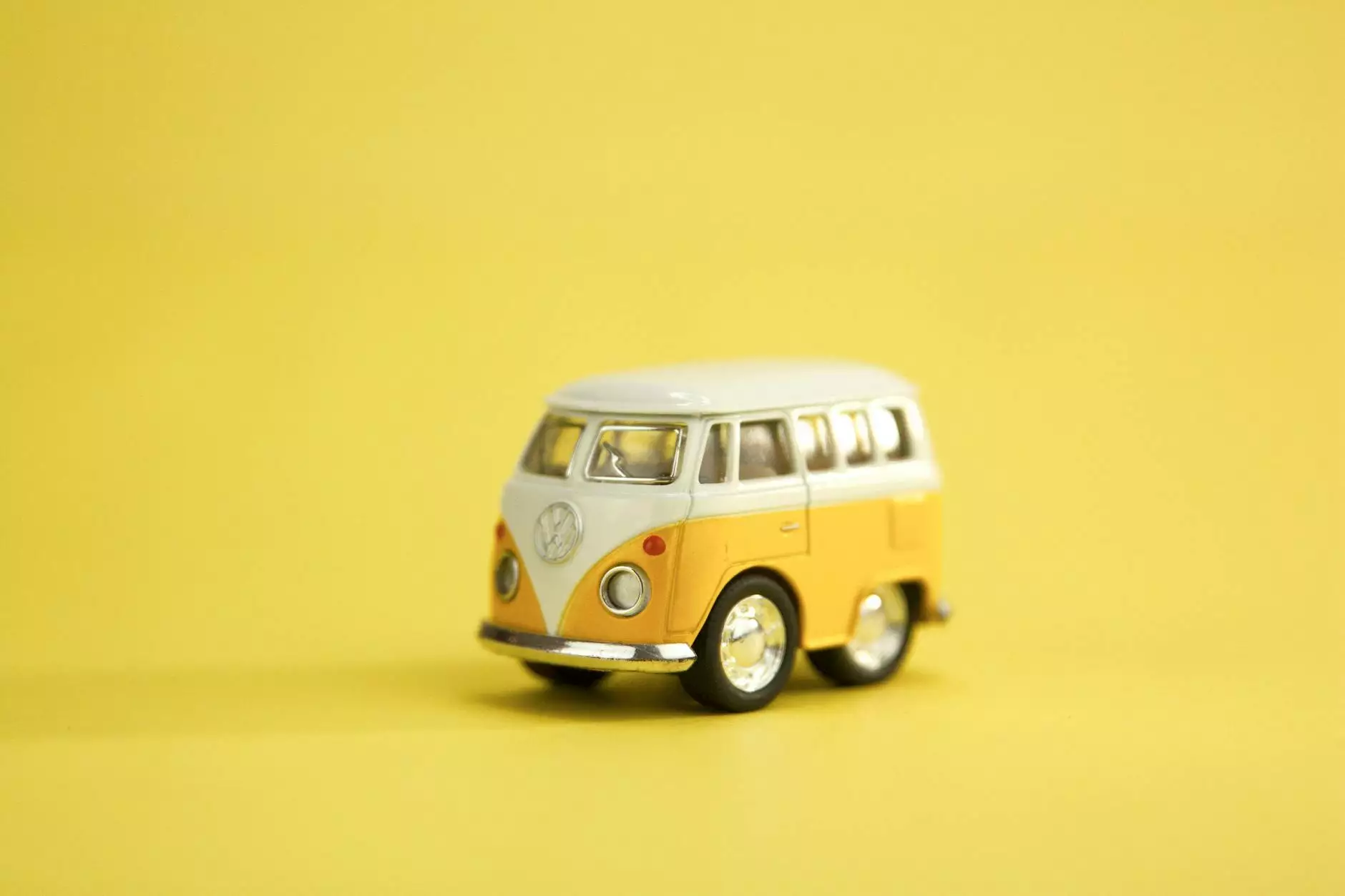
Metal die casting is a sophisticated technique used in manufacturing that allows for the production of intricate shapes with high dimensional accuracy. This article aims to delve deep into the advantages, processes, and applications of metal die casting, highlighting its significance in modern manufacturing. At DeepMould, we specialize in providing tailored solutions for your die casting needs, ensuring quality and efficiency.
What is Metal Die Casting?
Metal die casting is a manufacturing process that involves forcing molten metal into reusable molds (also known as dies). This method is widely used for its ability to create complex parts with outstanding accuracy and repeatability. Industries benefit tremendously from this process due to the following features:
- High Production Rates: Once a die is manufactured, thousands of parts can be produced in a short amount of time.
- Excellent Surface Finish: Metal die casting results in parts that have a smooth surface, requiring minimal finishing.
- Precision and Tolerance: The process can achieve tight tolerances, crucial for industries such as automotive and aerospace.
Types of Metal Die Casting
In the realm of metal die casting, there are several types recognized for their specific applications and manufacturing characteristics:
1. High-Pressure Die Casting
High-pressure die casting is the most common form of die casting. It involves injecting molten metal into a die under high pressure, often resulting in high-quality parts. This method is particularly useful for zinc, aluminum, and magnesium alloys.
2. Low-Pressure Die Casting
Low-pressure die casting is similar to high-pressure methods but operates at lower pressures, making it ideal for larger castings. This method minimizes porosity and defects in casted items.
3. Gravity Die Casting
This method utilizes gravity to fill the die with molten metal. It’s less expensive compared to pressure die casting but is often used for less complex or heavier items.
The Metal Die Casting Process
The metal die casting process can be broken down into several key steps:
- Die Preparation: Dies are prepared and coated with lubricant to facilitate molten metal flow.
- Melting the Metal: Raw metal is melted in a furnace to reach its liquid state.
- Injecting the Metal: The molten metal is injected into the die at high speed and pressure.
- Cooling: The part cools and solidifies within the die.
- Die Opening: The die is opened to release the finished casting.
- Trimming and Inspection: Excess material is trimmed off, and quality checks are conducted.
Benefits of Metal Die Casting
The advantages of employing metal die casting in manufacturing are numerous:
1. Cost Effectiveness
High-volume production through metal die casting significantly reduces the cost per unit. The initial setup cost for creating a die can be high, but it pays off with larger production runs.
2. Enhanced Durability
Components produced via die casting are often more durable than those from other manufacturing techniques. The metals used possess excellent structural properties, making them suitable for demanding applications.
3. Design Flexibility
Designers can create intricate shapes that would be difficult or impossible to achieve with other processes. This flexibility allows for innovative product designs.
4. Environmental Considerations
Die casting is an environmentally efficient process; it produces minimal waste, and the scrap metal can be recycled, contributing to sustainability efforts.
Applications of Metal Die Casting
Metal die casting is widely employed across various industries, underscoring its versatility:
1. Automotive Industry
In the automotive sector, components such as engine blocks, transmission cases, and other critical parts are manufactured using die casting. The precision and strength of die-cast components are essential for performance and durability.
2. Aerospace
The aerospace industry takes advantage of die casting for parts that require lightweight yet sturdy materials, such as brackets and housings.
3. Electronics
High-quality enclosures for electronic devices are produced using die casting. This method ensures that components meet strict electromagnetic interference standards.
4. Appliances
Consumer appliances, including kitchen gadgets and fixtures, often utilize die casting to produce both functional and aesthetic elements.
Conclusion
In conclusion, metal die casting is a crucial manufacturing process that provides numerous benefits, from cost savings to design flexibility. Its application across industries such as automotive, aerospace, electronics, and appliances showcases its versatility and efficiency. At DeepMould, we are dedicated to exploring the potential of this manufacturing method, providing our clients with innovative casting solutions that meet their specific needs.
To learn more about how metal die casting can add value to your projects, visit us at DeepMould today!