Mastering Tooling for Injection Molding: A Comprehensive Guide
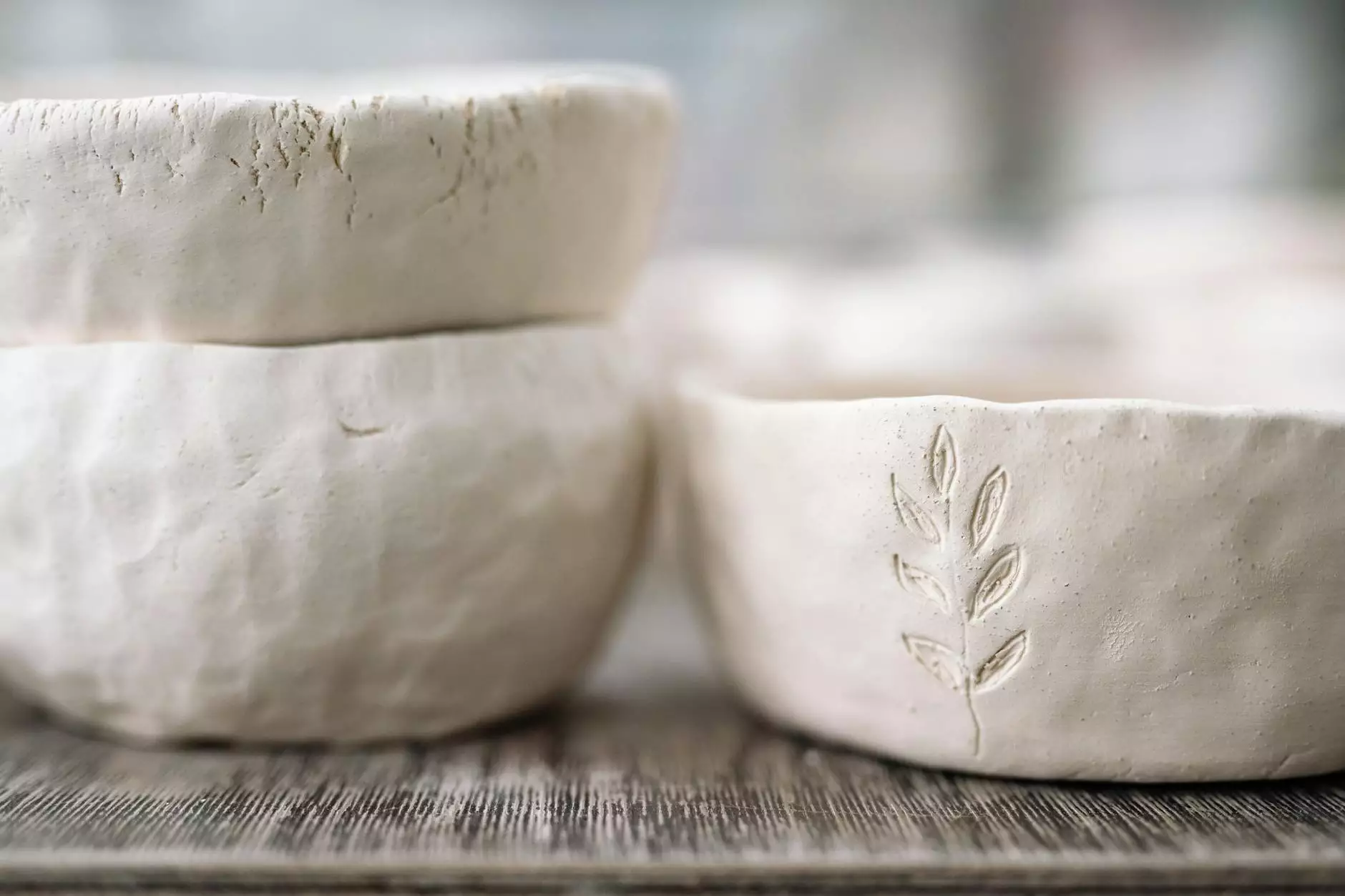
In the dynamic realm of manufacturing, tooling for injection molding plays a pivotal role, particularly for metal fabricators who require precision and reliability in their production processes. This article delves deeply into the various aspects of tooling for injection molding, providing valuable insights that can empower businesses and enhance their understanding of this crucial element in manufacturing.
Understanding Injection Molding
Injection molding is a manufacturing process used for producing parts by injecting molten material into a mold. Primarily utilized with thermoplastics and thermosetting polymers, injection molding is a favored process due to its capability to create complex shapes and high-volume products with significant precision.
How Injection Molding Works
The process involves several key steps:
- Material Preparation: Raw plastic materials are first prepared, which may involve granulating them.
- Melting: The prepared materials are heated until they reach a molten state.
- Injection: The molten plastic is injected into a mold under high pressure.
- Cooling: The injected material is allowed to cool and solidify in the mold.
- Demolding: Once solidified, the mold is opened, and the finished part is ejected.
The Importance of Tooling in Injection Molding
User-friendly and effective tooling is essential in injection molding as it directly impacts the quality of the final product, production efficiency, and cost-effectiveness. High-quality tooling can lead to:
- Increased productivity due to faster cycle times.
- Enhanced precision in part production, reducing waste.
- Lower overall manufacturing costs through improved efficiency.
- Greater design flexibility, allowing for innovative product designs.
Factors Influencing Tooling for Injection Molding
When considering tooling for injection molding, it is crucial to understand various influencing factors:
- Material Choice: The type of material being used can affect tooling design and fabrication.
- Mold Design: A well-thought-out mold design can enhance efficiency and quality.
- Molding Cycle Time: Effective tooling can significantly reduce cycle times.
- Maintenance: Regular maintenance of tooling ensures longevity and optimal performance.
Types of Tooling for Injection Molding
There are various types of tooling used in injection molding, each serving a specific purpose:
1. Prototype Molds
Prototype molds are often used for initial testing and development of a new product. They are typically made from softer materials and can be produced quickly for short runs, allowing for rapid iteration before final tooling is established.
2. Production Molds
Production molds are built for high-volume manufacturing. These molds are crafted from durable materials to withstand the rigors of large-scale production. They ensure consistent quality and precision across thousands or millions of units.
3. Insert Molds
Insert molding involves the use of pre-formed components or inserts within the mold. This technique allows for the integration of different materials or components into a single part, enhancing functionality and reducing assembly time.
4. Hot Runner Molds
Hot runner molds utilize a heated system to keep the plastic in a molten state as it flows through the runners to the cavity. This reduces waste and cycle time, making it a popular choice for high-volume production.
Design Considerations for Tooling
The design of tooling for injection molding is critical to the success of the manufacturing process. Below are some considerations that should beake during the design phase:
- Tolerances: Set acceptable tolerances for part dimensions and features to ensure functionality.
- Cooling Systems: Design effective cooling channels to minimize cycle time.
- Mold Flow Analysis: Use simulations to predict how the melted material will flow in the mold.
- Ease of Maintenance: Design molds with ease of access for maintenance and repair in mind.
Material Selection for Tooling
Choosing the right materials for tooling can significantly affect production efficiency and the quality of the final product. Common materials include:
- Steel: Known for its durability and strength, steel molds are ideal for high-volume production.
- aluminum: Lighter and easier to machine than steel, aluminum is often used for prototype molds but can also be used for lower-volume production.
- Composite Materials: These materials are becoming popular for their lightweight and customizable properties.
Tooling Maintenance and Care
Proper maintenance of tooling is crucial for longevity and performance. Regular inspection and cleaning can prevent costly downtime and ensure consistent production quality:
- Routine Inspections: Regular checks for wear and tear help identify potential issues before they escalate.
- Cleaning: Keep the molds clean to avoid contamination that can affect product quality.
- Proper Storage: Store molds in a controlled environment to prevent rust and damage.
Future Trends in Tooling for Injection Molding
The field of tooling for injection molding is continually evolving. Some emerging trends include:
- 3D Printing: This technology is revolutionizing mold making by significantly reducing lead times.
- Smart Manufacturing: The integration of IoT in tooling can lead to more efficient and automated processes.
- Sustainable Practices: The focus on eco-friendly materials and processes is becoming more prominent in tooling design.
Conclusion
Tooling for injection molding is a critical aspect of the manufacturing landscape, especially for metal fabricators. By understanding the various forms of tooling, maintenance needs, and future trends, businesses can significantly enhance their production processes, improve quality, and reduce costs. In conclusion, investing in quality tooling not only optimizes production but also propels a business towards operational excellence and sustainability.
Contact DeepMould for Your Tooling Needs
If your business is looking to enhance its injection molding processes, consider reaching out to DeepMould for expert insights and quality tooling solutions tailored to your specific requirements.