Unlocking the Power of Tooling Molds: The Cornerstone of Precision Metal Fabrication
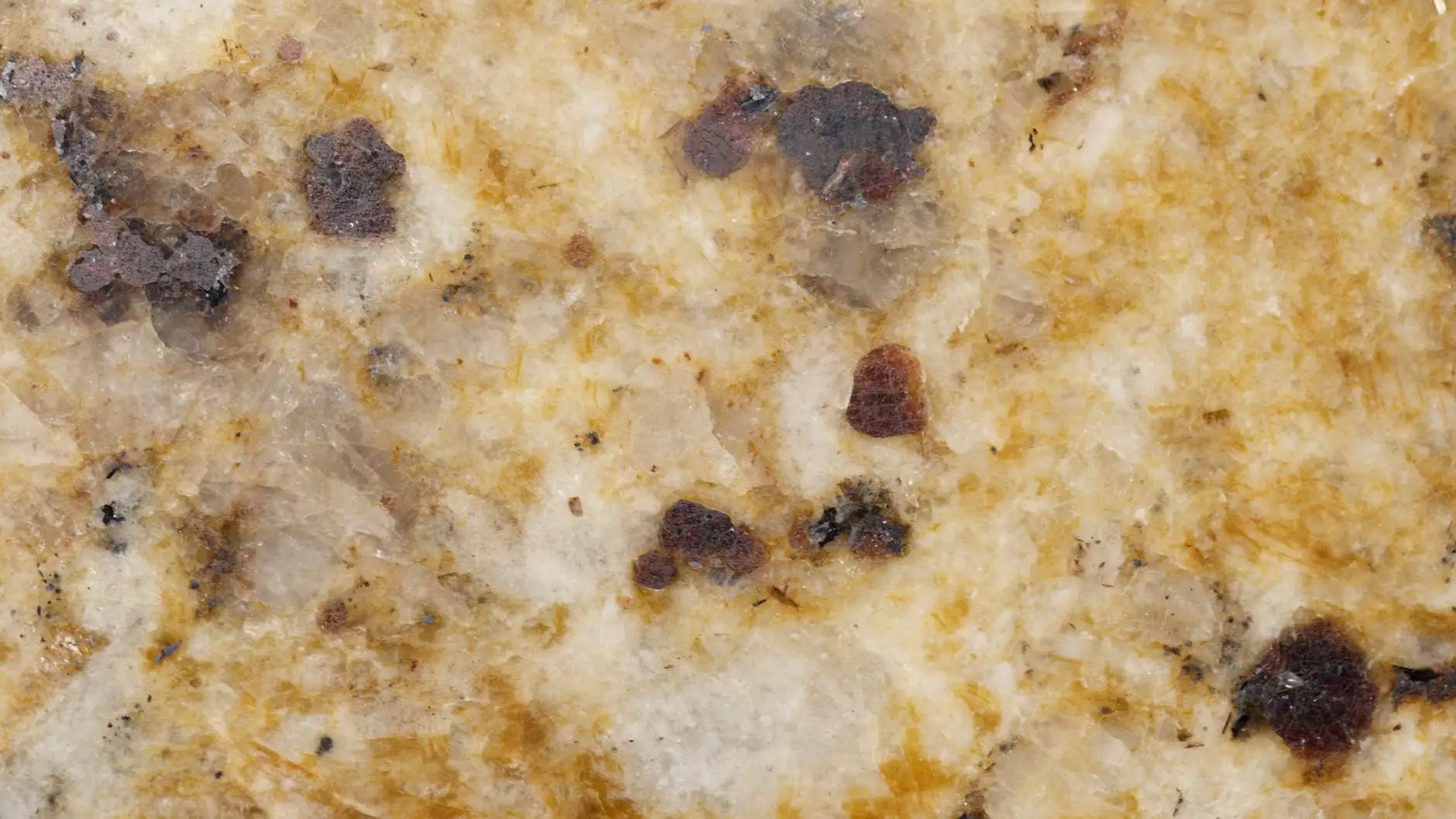
In the rapidly evolving world of manufacturing, tooling molds stand out as an indispensable element that underpins efficiency, precision, and scalability. Whether producing complex automotive components, electronic housings, or consumer products, the quality and design of tooling molds directly influence the final output, productivity, and profitability of manufacturing operations. As one of the leading specialists in metal fabrication, DeepMould.net exemplifies excellence in engineering and precision manufacturing dedicated to advancing the industry standard.
Understanding the Role of Tooling Molds in Metal Fabrication
At its core, a tooling mold is a carefully engineered and meticulously crafted component used to shape raw materials—primarily metals—into desired forms through processes such as injection molding, die casting, or stamping. The primary purpose of these molds is to facilitate repetitive manufacturing with utmost precision, durability, and consistency. High-quality tooling molds are essential to achieving tight tolerances and surface finishes that meet rigorous industry specifications.
Types of Tooling Molds in Metal Fabrication
- Injection Molds: Used predominantly in plastic and metal injection molding, these molds allow complex parts to be produced rapidly and accurately.
- Die Cast Molds: Designed for die casting processes, these molds are robust and enable high-volume production of metal parts like aluminum and zinc components.
- Progressive and Transfer Dies: Utilized in stamping, these molds streamline the fabrication of sheet metal parts through multiple station operations.
- Compression and Transfer Molds: Employed in molding thermoset plastics and composites, ensuring high precision and mechanical integrity.
Design Excellence: The Foundation of Superior Tooling Molds
The process of designing tooling molds is both an art and a science, demanding innovative engineering and detailed planning. Successful mold design hinges on understanding material behavior, thermal management, and mechanical constraints. Advanced CAD (Computer-Aided Design) and CAE (Computer-Aided Engineering) tools are used to simulate and optimize mold performance before manufacturing begins, mitigating costly errors and reducing time-to-market.
Critical considerations in tooling mold design include:
- Material selection: Using high-grade steel, aluminum, or other alloys enhances longevity and performance.
- Cavity and core design: Precision-engineered cavities ensure product consistency and dimensional accuracy.
- Cooling system integration: Efficient cooling channels are vital to controlling cycle times and preventing warping or defects.
- Surface finish and texture: Surface treatments improve release properties and aesthetic appeal of molded parts.
The Manufacturing Process of Tooling Molds
Manufacturing tooling molds involves multiple sophisticated processes that demand utmost precision:
1. Material Machining
High-precision CNC (Computer Numerical Control) machines mill, drill, and shape raw steel or aluminum blocks into mold components. This stage emphasizes tight tolerances and surface finishes.
2. Heat Treatment
To enhance wear resistance and structural integrity, mold components undergo heat treatments such as hardening and tempering, ensuring durability during high-volume production.
3. Electro-Discharge Machining (EDM)
EDM allows for complex geometries and intricate details in mold cavities, enabling the production of highly detailed and precise molds.
4. Surface Finishing
Processes like polishing, texturing, and coating improve the mold’s surface quality, facilitate part release, and extend mold life.
Optimization and Innovation in Tooling Molds
In today’s competitive landscape, innovation is key to maintaining manufacturing advantages. Leading metal fabricators focus on integrating new technologies and methodologies into tooling molds development, including:
- Rapid Prototyping: 3D printing and additive manufacturing allow for quick validation and iteration of mold designs.
- Modular Mold Design: Swappable components and modular systems reduce downtime and facilitate easier maintenance or redesigns.
- Smart Molds: Embedding sensors for real-time monitoring of temperature, pressure, and wear enhances production control and predictive maintenance.
- Eco-Friendly Practices: Using sustainable materials and energy-efficient processes minimizes environmental impact while maintaining high quality.
The Significance of Tooling Molds in Modern Manufacturing
Modern manufacturing relies heavily on well-crafted tooling molds for several reasons:
- Cost Efficiency: High-quality molds enable high-volume production with minimal defects, decreasing waste and lowering unit costs.
- Product Consistency: Precise molds ensure uniformity across large production runs, maintaining brand quality standards.
- Time Savings: Durable molds with fast cycle times accelerate production timelines, meeting market demands swiftly.
- Design Flexibility: Advanced mold designs facilitate complex geometries and innovative product features that differentiate brands.
Why Choose DeepMould.net for Tooling Molds?
As a leader among metal fabricators, DeepMould.net offers unmatched expertise in the design and manufacturing of tooling molds. Our commitment to innovation, quality, and customer satisfaction positions us as your ideal partner to elevate your manufacturing processes. Here are some reasons to collaborate with us:
- Extensive Experience: Decades of expertise in precision mold fabrication for diverse industries.
- State-of-the-Art Equipment: Utilizing cutting-edge CNC, EDM, and additive manufacturing technologies.
- Customized Solutions: Tailoring molds to specific requirements for optimal performance and efficiency.
- Quality Assurance: Rigorous testing, inspection, and adherence to international standards.
- End-to-End Service: From initial design to post-production support, we provide comprehensive solutions.
The Future of Tooling Molds: Embracing Innovation and Sustainability
The future of tooling molds is poised to be shaped by technological advancements and sustainable practices. Innovations like artificial intelligence in mold design, machine learning for predictive maintenance, and environmentally friendly materials are revolutionizing the industry. As manufacturers aim for even higher precision, efficiency, and eco-consciousness, the role of advanced tooling molds becomes more crucial than ever. Companies like DeepMould.net are at the forefront of integrating these transformative trends to deliver cutting-edge solutions tailored to tomorrow’s manufacturing needs.
Conclusion: The Strategic Importance of Tooling Molds in Manufacturing Success
In the landscape of modern manufacturing, tooling molds are not merely tools but strategic assets that define the quality, efficiency, and innovation capacity of any production enterprise. High-quality, well-designed molds empower manufacturers to produce complex, durable, and high-precision parts while optimizing costs and reducing lead times. As an industry leader specializing in metal fabrication, DeepMould.net continually strives to advance mold technology, ensuring our clients stay ahead in fiercely competitive markets. Embrace the future of manufacturing excellence through expert craftsmanship, relentless innovation, and unwavering quality—beginning with the right tooling molds.